Fittings That Last: How to Find Durable Solutions for Industrial Use
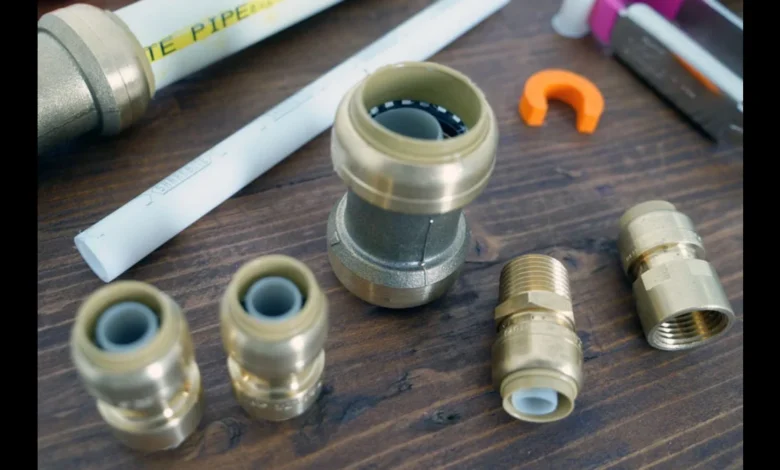
Most Parts used for industrial fitting must withstand extreme temperatures, pressure, and corrosive conditions. As a fitting is an important connector in many systems, it plays an important role in fitting industrial use to avoid costly accidents and downtime. Whether plumbing, HVAC, or fluid transport systems, long-lasting fittings prolong the life of industrial equipment and enhance performance. The following article considers several key factors in selecting durable, long-lasting camlocks for your industrial activities.
Compatibility with Media
Fittings should be chosen based on the media type flown inside. For example, if aggressive chemicals or gases are transported to your system, metal fittings with special coatings may be used to prevent corrosion and degradation. In these cases, fluoropolymer coatings on stainless steel offer extra protection. That way, a fitting resistant to the media with which it comes into contact can continue to function much longer, thereby reducing the replacement frequency.
Pressure and Temperature Ratings
Industrial fittings are very often subjected to extreme changes in pressure and temperature. To avoid system failure, selecting fittings whose rating is equal to or above your system’s operational pressure and temperature is important. Most fittings have specific ratings for pressure and temperature based on the materials used and the construction method. For example, stainless steel can withstand high pressures and extreme temperatures much better than plastic or brass. Applications in high-temperature settings would be required to make fittings from metals or alloys such as Inconel or titanium.
Corrosion Resistance
Due to their high resistance to corrosion, stainless steel are successfully used in the marine, oil, and chemical sectors. Galvanized steel also performs very well and a great option when a lower-cost alternative is needed. Anti-corrosive fitting selections will reduce not only the maintenance costs but also the safety hazards.
Maintenance Requirements
This is another point: Ease of maintenance of the fitting is to be considered while selecting industrial fittings. The fittings that require constant inspections, repairs, or replacements increase labor costs and system downtime. Select those low-maintenance fittings designed with self-sealing or anti-leak properties. For instance, threaded fittings can easily be taken apart and inspected compared to welded or soldered. Ensuring the fitting can easily be maintained will help foster greater efficiency in your industrial systems.
Certification and Standards Compliance
Resistance fittings should, to the best of their capability, meet the standards and various certifications laid down by the industry so that they are assured to be safe and operational in specified applications. Among the globally accepted standards are ISO, ASTM, and ASME. Choose fittings with certification for the operating environment and the media they will use. That way, it will be long-lasting and compatible with each other. This can help you avoid potential failure from incompatible parts that may present a safety hazard. Check for standard compliance- a standard that applies to your industry, such as NSF certifications on potable water systems.
Type of Connection
The connection type among fittings and other components is related to various aspects of a system. The types include threaded, welded, flanged, and compression fittings. Threaded fittings can be installed and replaced easily and may require periodic maintenance to avoid leaking. On the other hand, welded fittings are more permanent but cumbersome to replace in case anything goes wrong. Making a proper choice between these connection types on your needs for operation and expected load can extend the life of your fittings.
Selection of durable fittings is crucial for any industrial application; this helps ensure your systems’ safety, reliability, and longevity. You can choose between performance enhancement and maintenance cost-cutting by considering material selection, corrosion resistance, pressure ratings, and industry certifications. The right fitting camlocks ensure improved operational efficiency and avoid unexpected failures that may bring production to a standstill. A quality investment in fittings will now mean long-term savings plus much more peace of mind in industrial settings.